Grinding
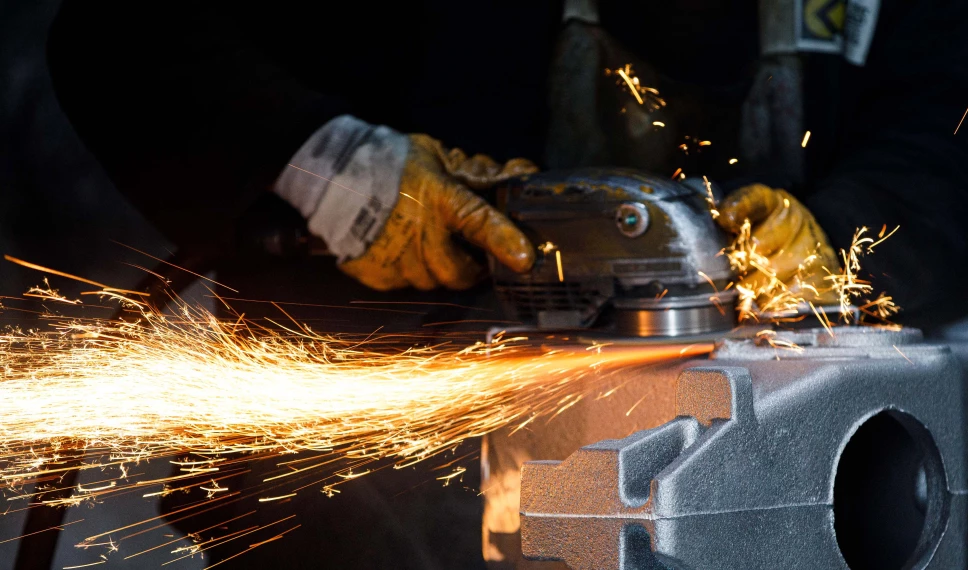
Grinding, which is one of the main activities of the metal production sector, is a process applied for pre-cleaned decoiler parts to enter the desired form. The process, which has types such as automatic grinding, external grinding, fixed grinding, circular grinding, strip grinding and internal grinding, helps to free and shape casting parts from redundancy. The parts passed through the grinding process are sent to the cleaning machines and the cleaning process is performed according to the nature of the part. Kutes Metal, which is the pioneer of its sector, makes your castings perfect with its grinding services.
Casting grinding processes are applied in many different areas, from automotive to railway, from construction to air conditioning systems. The grinding methods used by Kutes Metal are as follows:
Automatic Grinding
Kutes Metal performs automatic casting operations for high numbered casting parts with 2 PS Auto Grinding 400i (1 kg - 20 kg) and 2 PS Auto Grinding 400i (20 kg - 70 kg). Automatic grinding machines operating on CNC principle stand out with high and stable standards as well as series grinding. Automatic grinding machines, which can perform high quality grinding for all casting parts, thus achieve the same standard in all parts of high-quantity batches.
External Grinding
With 4 external grinding stations and automatic machines, Kutes Metal performs the grinding operations to be applied to the outer surface of the casting parts flawlessly. Grinding of multi-angle, long and wide cast parts and products produced in low quantities is also carried out by specialist operators in the field.
Fixed Grinding
Fixed grinding operations are performed at 2 different stations of Kutes Metal by 4 specialist operators in each shift. Machines located in Kutes Metal's fixed grinding stations can effectively grind even difficult casting parts with a single feeder input or poor feeder inputs, thanks to their dual grinding wheels.
Circular and Strip Grinding
Circular grinding is a process applied to casting fine hackle parts with low kilograms and high numbers. Hackle parts are first cleaned by circular grinding and made without a hackle. Then the feeder entries of the cast parts sent to the fixed grinding machine are also processed in the fixed grinding machine.
Strip grinding is responsible for the processes of grinding unbroken feeders of cast parts and manual grinding of sections that the machine cannot reach. With 2 circular and 1 strip grinding stations, Kutes Metal provides effective grinding of even hackle-free, low-kilogram, high-quantity and demanding cast parts.
Internal Grinding
At Kutes Metal, the last stop for casting parts in the grinding process is one of 3 different internal grinding stations. Parts that have a width above the capacity of automatic machines are cleaned by manual internal grinding. Cast parts that have completed the external grinding process get rid of the hackle and excess left in their internal parts by the internal grinding method, and with this process, the grinding process ends.
What Is Final Cleaning?
Final cleaning is a method performed after internal and external grinding operations and applied to get rid of the excess that sticks to the cast parts. Kutes Metal performs final cleaning with 2 ball cleaning machines and 1 pressure cleaning machine.
Parts that are heavy in kilograms, in danger of crushing or breaking, are cleaned in a hanging cleaning machine. Parts with low weight, excess quantity and no risk of breaking or crushing are processed in the drum cleaning machine. During the process, the small-sized steel balls in the machines come into contact with the grinding marks and clean the casting parts.
Pressure cleaning machine is used in cases where hanger and drum machines are insufficient. A pressurized ball process is applied to the interior of the cast parts, thus eliminating any excess that cannot be cleaned in the ball machine.
Kutes Metal, which also stands out with its eco-friendly policies, eliminates metal dust released during the grinding process with state-of-the-art air filters and cleaning systems. In this way, Kutes Metal, which prepares a healthy and sterile environment for its employees, also prevents the damage of nature due to metal waste.