Melting
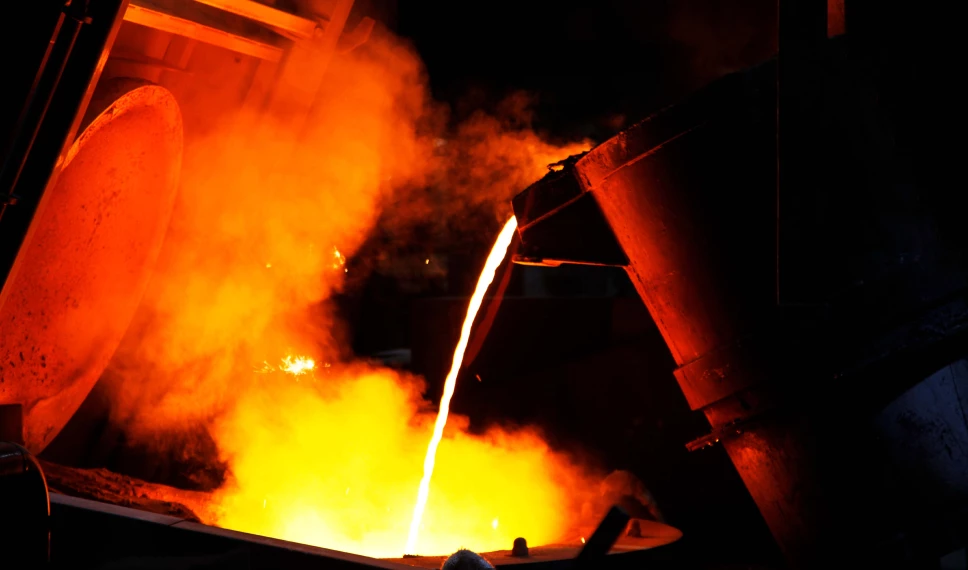
Kutes Döküm has the melting and casting capacity of 16 tons/hour with 8 inductotherm dual track melting furnaces. Kutes Döküm has “4” (5 tons/hour) melting furnaces on the melting platform feeding the HWS (Heinrich Wagner Sinto) line, and “4” (3 tons/hour) melting furnaces on the melting platform feeding our Georg Fischer line.
What İs The Process of Melting?
The melting process is done by the electric induction method, which is the most environmentally friendly and efficient method known in our furnaces. A strong magnetic field is created when electricity is passed through the coil in the oven, which is wound on a coil. This magnetic field increases the heat of the metal to be melted along with the electric resistance. In this way, melting is achieved by the electric induction method. In this method, where you can get a high yield, the losses of the substance are low, while a higher quality product is obtained. During melting, the process of mixing alloys takes place on its own. This method provides superiority in operating conditions and melting is performed in a cleaner environment. Because fuel gases are not used in this environmentally friendly method, environmental pollution also does not occur.
The casting automat in our HWS line works with Siemens S7-300-Technology PLC system which is fully automatic in accordance with Industry 4.0 principles. Thanks to the ‘2‘ state-of-the-art camera, which constantly monitors ductile iron and peak casting, the temperature, casting time and weight of each spilled part can be monitored. HWS line melting is performed by horizontal molding. It has a multifunctional and compact design. Pot tipping options can be adjusted. The low-pressure casting system provides the perfect best solidification for casting. It also saves resources and energy. It reaches every point of sand by compressing the corners to the maximum. It does compression without binders. It also has high forming precision.
Our George Fischer line has Inductotherm Visipour P3 Automatic Tundish casting automaton. In the system working with the stopper-nozzle principle, stopper control is made by servo motor. The Georg Fischer line passes through the melting process. This system works according to Visipour P3 technology, which is predictive casting performance. These unheated systems are ideal for melting operations that require rapid alloy changes. These processes take place thanks to a stop rod casting mechanism using refractory lined tundish. Servo-driven stoppers are patented. It has the industry's most responsive and reliable bulk control. It is easy to maintain and thermally efficient.